Arc Screen
The arc screen is mainly used for the preliminary dewatering, de-mud, and de-sanding of materials with a relatively high liquid-solid ratio. Its structure mainly includes the feed box, screen surface, and under-screen collection hopper. The arc screen has a simple structure, but inappropriate choices often occur during equipment selection. The two most common situations are:
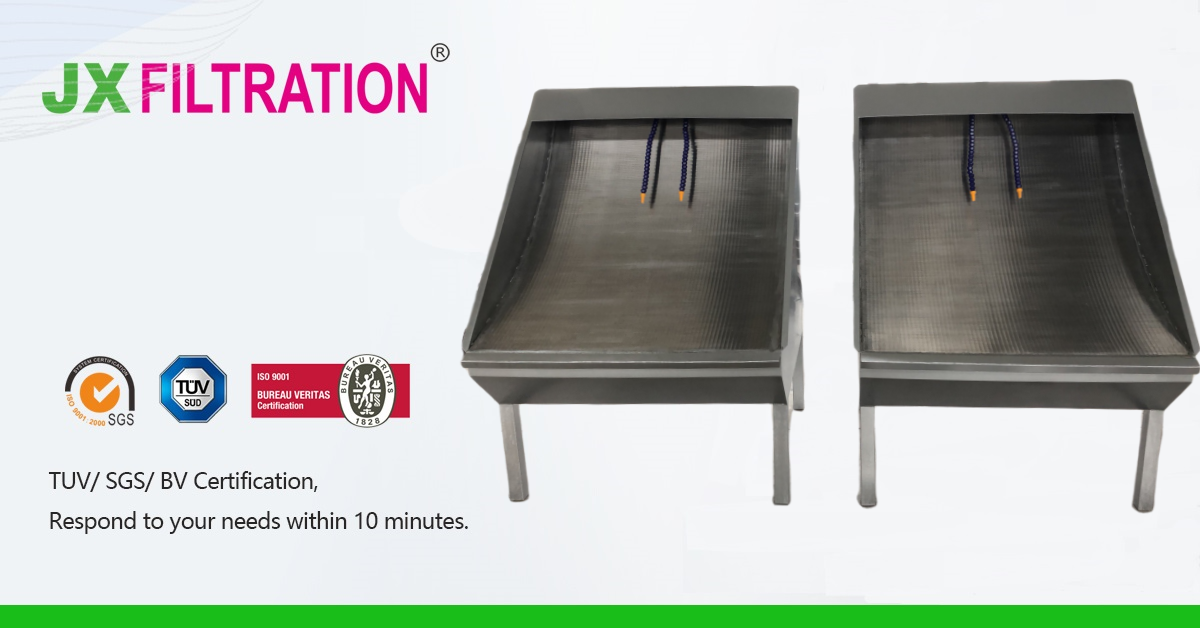
(1) Serious material stacking on the screen surface, poor material fluidity, reducing the effective area of the screen surface.
(2) Serious water running on the screen surface, failing to achieve the purpose of dewatering and de-mudding. The root cause of these two problems is a lack of understanding of the process parameters of the arc screen, such as determining the processing capacity.
When selecting the arc screen, the following four points should be fully considered:
- Feeding Method
The arc screen feed box can be pressure-fed or self-flowing, with self-flowing feed being predominant in coal preparation plants. In order to maximize the recovery of liquid in the feed, the inlet velocity of the arc screen must be maintained within a certain range. Generally, when the particle size is between 50-150μm, the inlet velocity of the arc screen is between 12-18m/s. In this case, pressure feeding is required.
The liquid recovery rate is related to the Reynolds number. The larger the Reynolds number, the greater the liquid recovery rate. In other words, the narrower the slot spacing, the greater the required average flow rate. The commonly used slot spacing is between 0.35~3mm, and the average speed of the screen surface is within the range of 3m/s. At this time, the inlet pressure head is 500mm, and adjusting the pressure head of the feed box can change the inlet velocity.
- Slot Size
The grading range of the arc screen is between 100-12000μm, and the grading of metallic minerals is between 200-3000μm. The arc screen can produce accurate particle size grading, even when the feed concentration reaches 50%. In contrast, the hydrocyclone is significantly affected by particle specific gravity and feed concentration. When the feed concentration is greater than 15% (volume), coarse particles will significantly enter the overflow. Meanwhile, the arc screen is lightweight and has low maintenance costs. Under low feed rates, the screen life is between 1000-2000h, and under high pressure, it is only 200-300h. Usually, changing the direction or flow direction of the screen to extend its service life. Of course, the service life of the screen depends on its own material and the nature of the material.
The size of the screened particle size depends only on the screening spacing, and the density of the solid, the viscosity of the liquid, and the average flow rate on the screen surface have little effect on the screened particle size. The feed concentration will affect the screening efficiency to a certain extent, and a feed concentration of 15%~40% is appropriate. The size of the screen slots can be determined based on the requirements for particle size in the bottom flow.
- Processing Capacity
After determining the feed velocity and slot spacing, the processing capacity of the screen is related to its open area. Considering the wear resistance of the screen, the width of the screen strip is generally not less than 1.5 times the slot spacing. The smaller the radius of the screen surface, the greater the centrifugal force acting on the liquid. In heavy medium dressing, the arc screen is often used together with the linear vibrating screen, with a slot spacing of 0.5mm, and the suspension removal capacity can reach around 100m³/(h*m²).
- Screen Surface Curvature
The selection of screen surface curvature is generally determined by the flow state of the material. If the curvature is too small, the slurry will stay on the screen surface for a short time, and some water and fine particles will run off the screen surface. If the curvature is too large, the discharge end of the screen surface is smooth, and the slurry flow rate decreases. Although it is beneficial for dewatering, the material is prone to pile up on the screen surface. The two problems mentioned at the beginning of this article are caused by improper curvature selection. The curvature of domestic arc screens is 45°, 53°, 60°. Of course, other curvatures can also be produced.
Any Requirements, Contact Us Now!
Kris
Email/Teams: kris@filtrationchina.com
Mobile/Whatsapp/Wechat: +86 18980776200
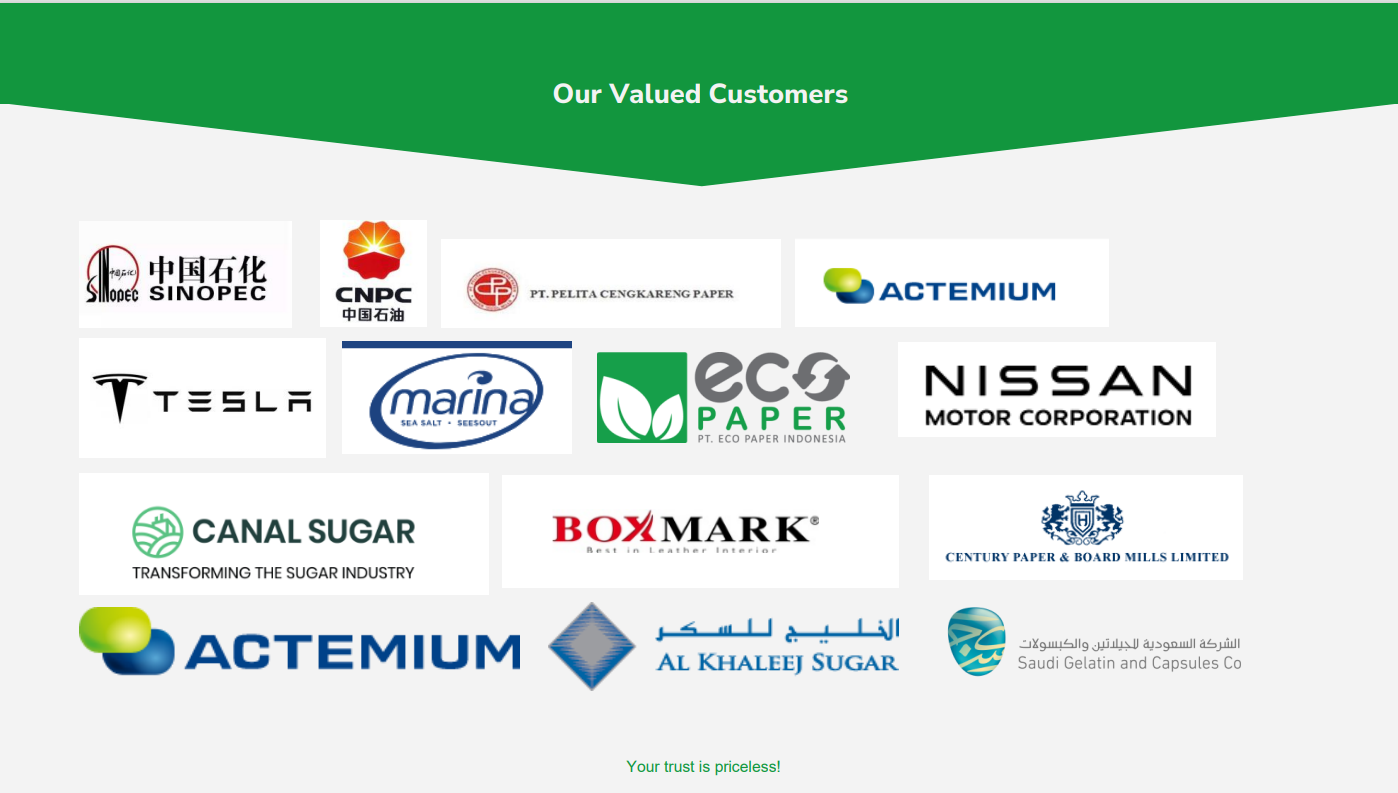